Shock tube
Shock tube is an experimental device that compresses and heats reactants instantaneously to a specified temperature and pressure through shock waves. Due to its uniform adiabatic non isentropic compression of the medium through incident and reflected shock waves, a wide range of experimental temperatures and pressures can be obtained by adjusting the velocity of the incident shock wave and the initial pressure of the experimental gas.
The high-pressure shock tube experimental system at Northwestern Polytechnical University is a High-pressure + Single pulse hybrid shock tube (as shown in Figure 1). After the shock wave is reflected in the shock tube, the temperature in the experimental area can reach 700-4000 K or even higher, with a pressure range of 0.01-10 MPa. The experimental time is generally 0.1-10 ms. Compared to conventional high-pressure shock tubes and single pulse shock tubes, there are two obvious advantages:
(1) The pressure bearing capacity has significantly increased, with a maximum pressure resistance of up to 10 MPa, allowing for Pyrolysis and ignition experiments with a wider range of experimental pressure conditions;
(2) Convenient and labor-saving, equipped with a two-way straight tube and a replaceable three-way section near the middle section of the low-pressure section, it can achieve both conventional high-pressure shock tube and single pulse shock tube forms. Experimental research can be conducted on ignition delay time and high-temperature pyrolysis characteristics of solid, liquid, and gas fuels under a wide range of operating conditions.
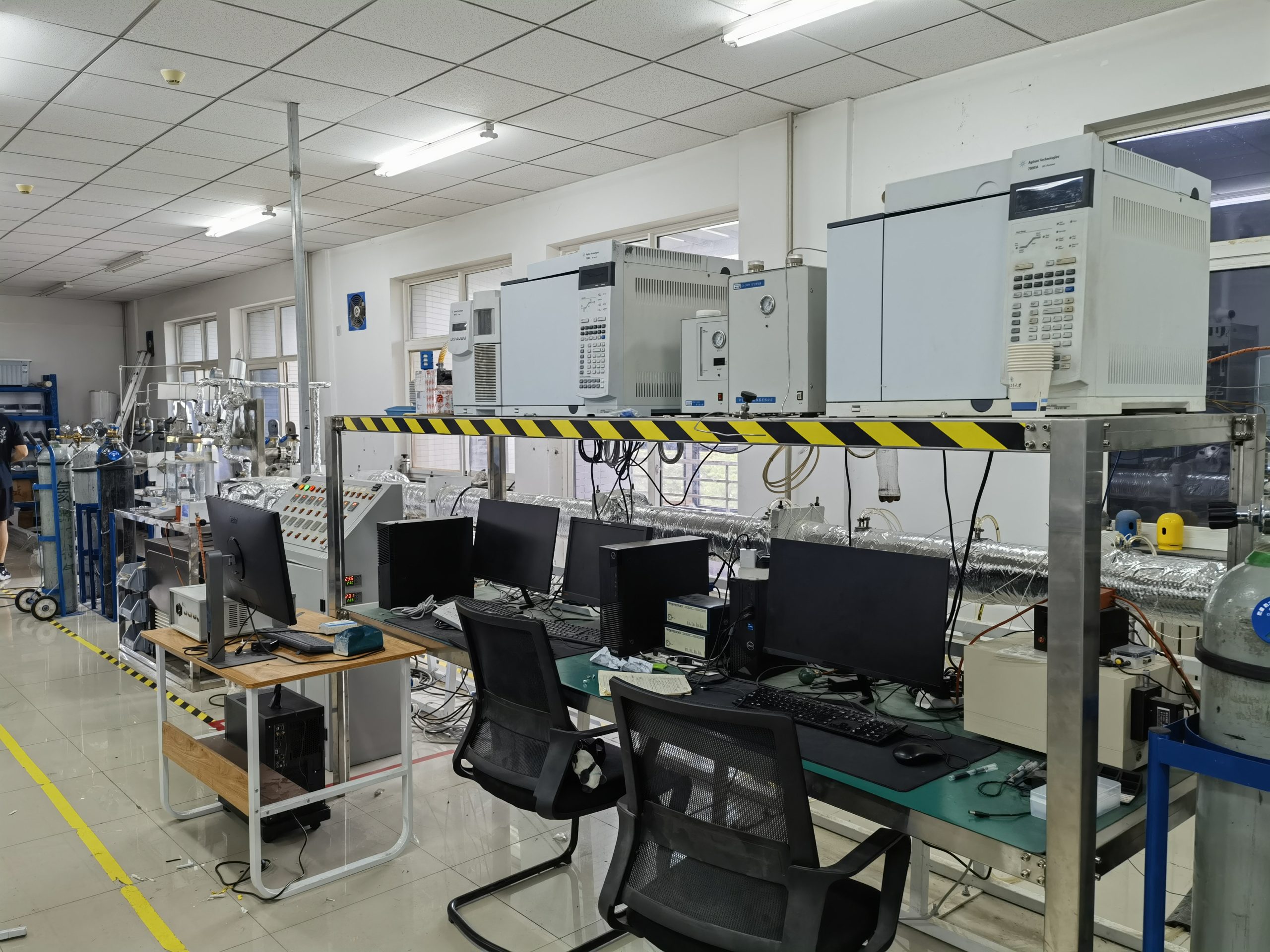
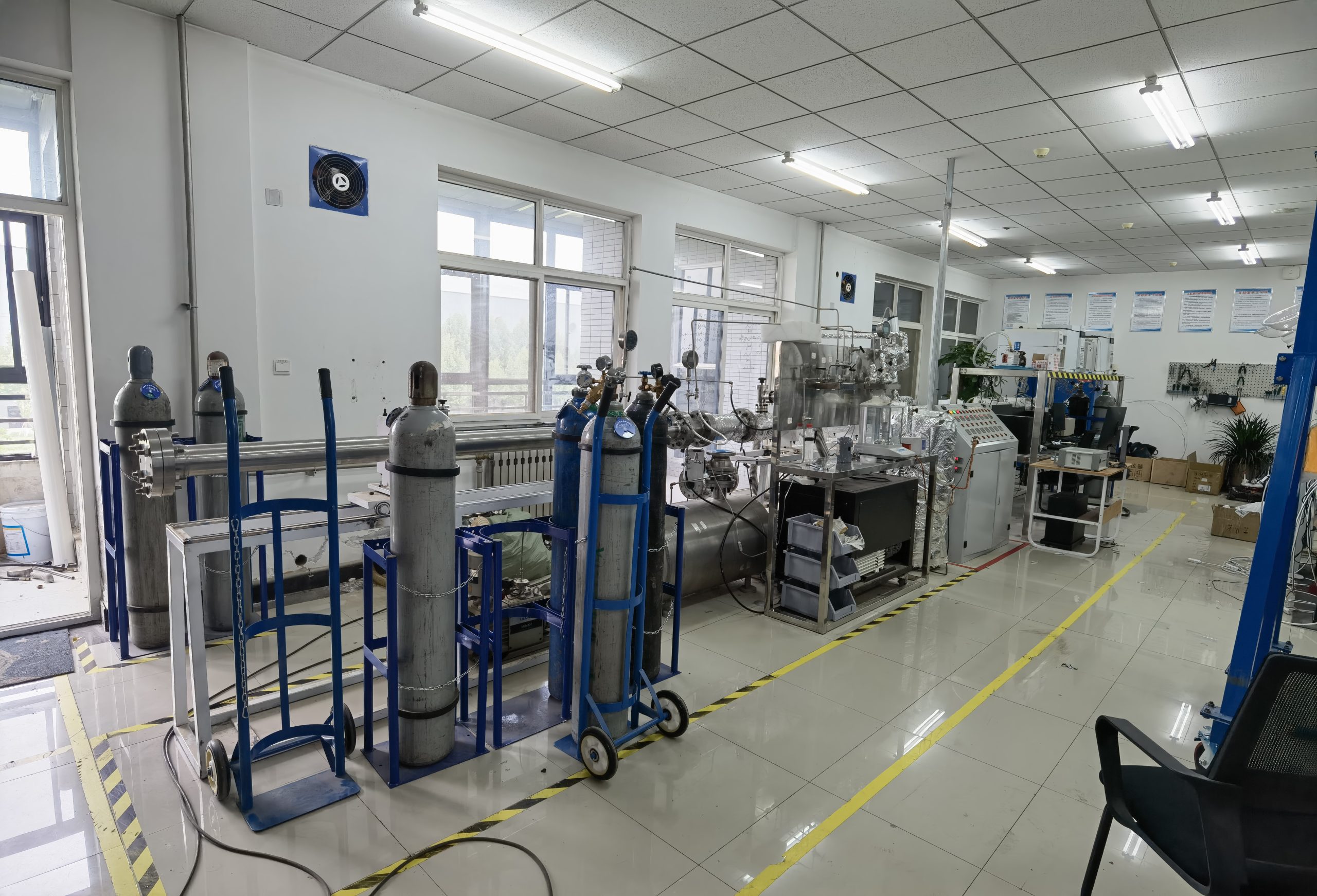
Fig. 1. Physical photos of the shock tube in NPU
The shock tube is made of 304 stainless steel material and is equipped with a driving section that is 5.6 meters long and has an inner diameter of 8.4 centimeters, as well as a driven section that is 6.0 meters long and has an inner diameter of 8.4 centimeters, which is the experimental testing section. The double-diagram intermediate section (length 0.4 m, inner diameter 8.4 cm) designed between the driven section and the driving section is used to achieve double membrane driven membrane rupture and generate incident shock waves. The vacuum system consists of two pumping systems, which are respectively suitable for atmospheric pressure (roughing pump, Agilent DS402 type) and high vacuum (turbo molecular pump) pressure environments. By combining these two pumps, a vacuum pressure of approximately 0-5 Pa can be achieved before each experiment. The pressure measuring equipment used in this facility has a range of 1000 torr (Inficon CDG160D). To measure the velocity of the incident shock wave, five piezoelectric pressure sensors (PCB P113B24) were arranged along the last 2.1 meters of the driven section. In order to adapt to the gas-phase testing of low vapor pressure fuels, the shock tube is equipped with heating belts and wrapped in asbestos shells, with temperatures up to 200 ℃. Additional heating elements and fiberglass insulation materials have been installed on the mixing tank and manifold to prevent any possible fuel condensation.Figure 2 shows a schematic diagram of a conventional high-pressure shock tube experimental system for conducting ignition delay time experiments on gas or liquid fuels using this system.
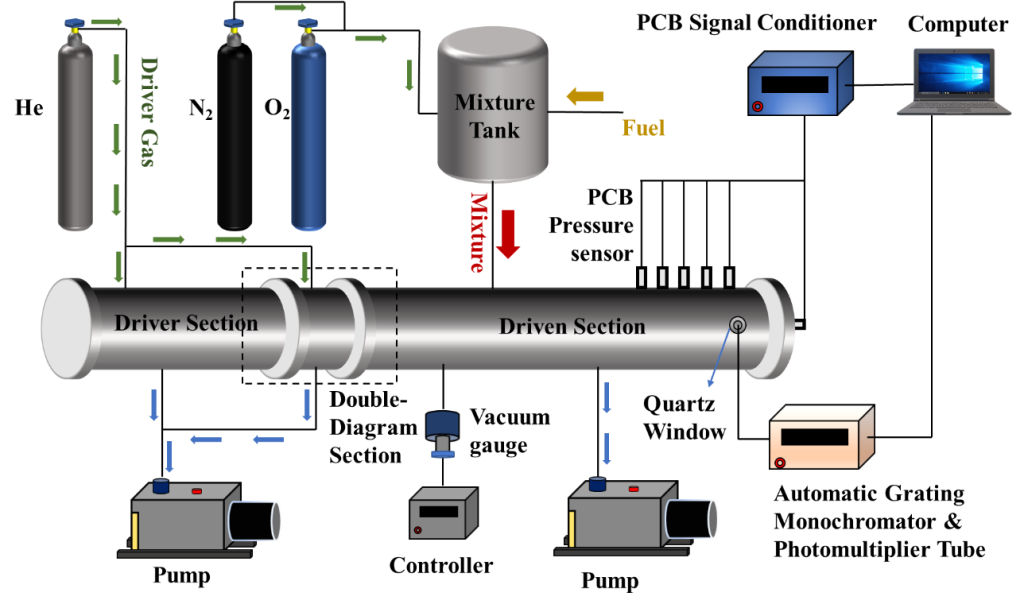
Fig. 2. Scheme diagram of high-pressure shock tube
By adding a dump tank to the conventional configuration, it is possible to absorb the subsequent reflected shock waves during the experimental process, enabling the use of a single shock wave to heat the fuel and conduct experimental research on the high-temperature pyrolysis characteristics of gas and liquid fuels. At the same time, a gas chromatograph (Agilent 7890 B) and a gas chromatography-mass spectrometer (Agilent 7890 B-5975 B) coupled with the equipment can be used to qualitatively and quantitatively analyze the pyrolysis products and explore the distribution law of the products concentration with experimental working temperature changes.
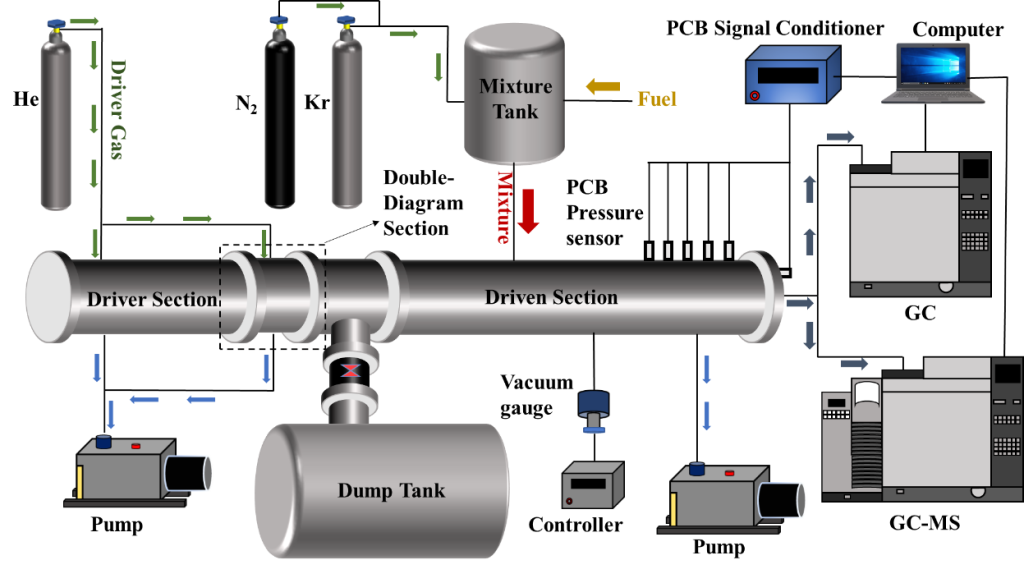
Fig. 3. Scheme diagram of single-pulse shock tube
In order to conduct experimental research on solid fuels, the end cover of the driven section was modified by adding a tray at its center position as shown in Figures 4 and 5 to hold solid fuel powder. During the experiment, when the shock wave passes through the tray, the solid fuel powder on the tray is lifted and evenly dispersed. Then, when the reflected shock wave passes again, the energetic material powder is instantly heated to the expected temperature, where ignition combustion and high-temperature pyrolysis occur.
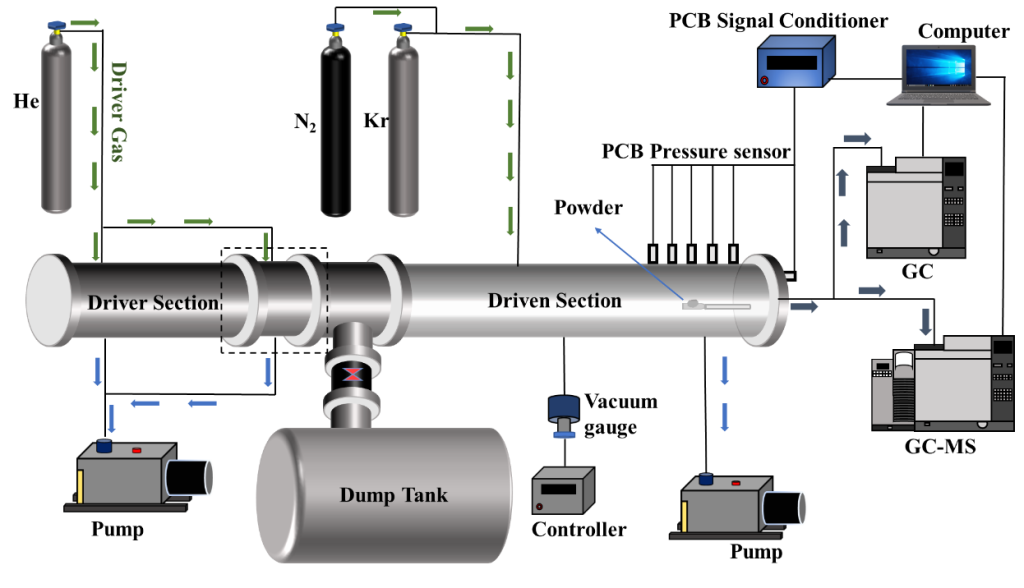
Fig. 4. Scheme diagram of single-pulse shock tube for powder
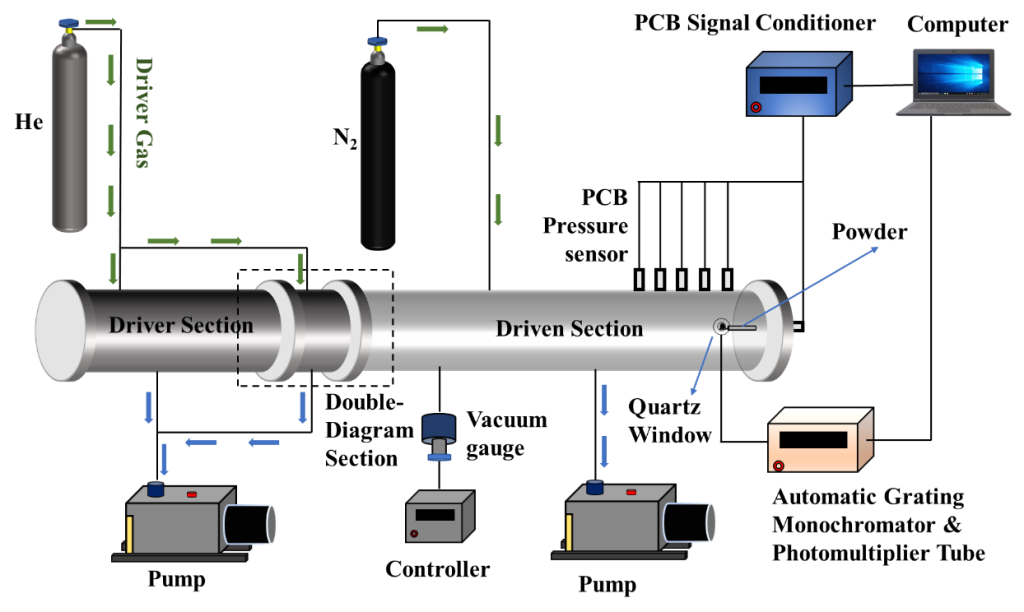