Combustion Models and Simulations
Introduction
Simulating the combustion of rocket propellants is essential for advancing propulsion technologies and optimizing combustion performance of aerospace vehicles. Our research includes developing high-fidelity numerical models that can simulate the complex chemical and physical interactions during propellant combustion.
Modeling for propellants
For solid propellants, we model the decomposition and combustion of HTPB, double-based, NEPE and other promising propellants, particularly for the evolution of burning surfaces by coupling gas and condensed-phase detailed kinetic mechanisms. For liquid propellants, we simulate atomization, evaporation, based on detailed gas-phase chemical kinetics to replicate real-world combustion conditions. In addition, we are exploring electrochemical reaction mechanisms with a view to model development of electronically controlled propellants.
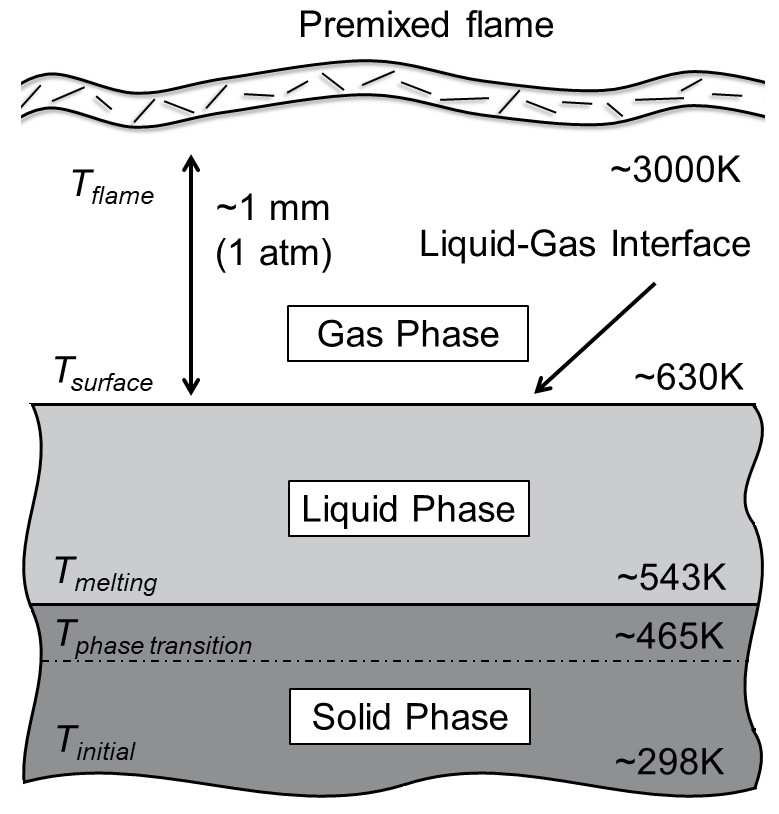
Fig. 1. Schematic chart of three-phase 1-D solid propellant mole coupled based on detailed kinetic mechanisms. (On working)
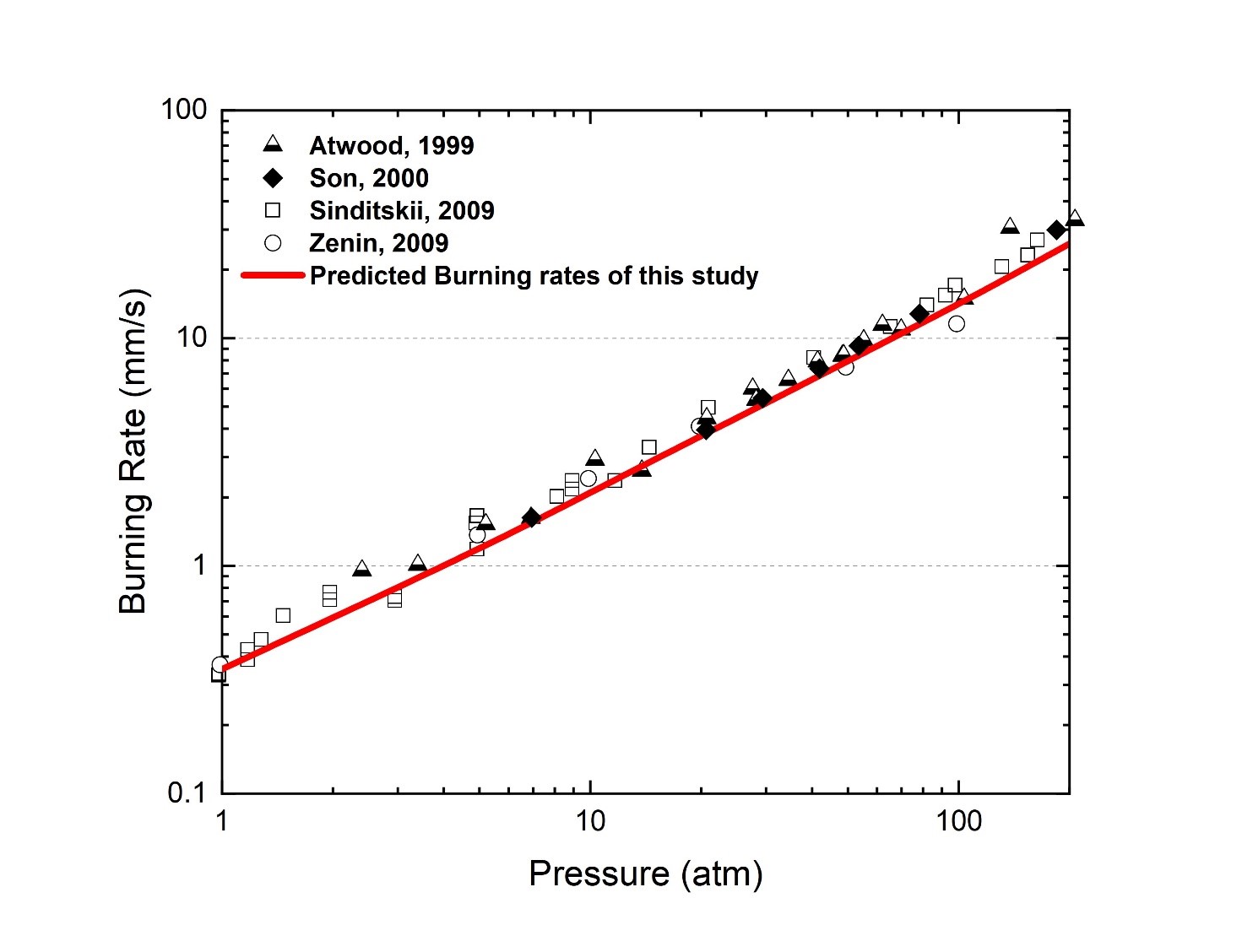
Fig. 2. Predicted burning rates of HMX monopropellant from 1-200 atm against experimental data. (On working)
Computational fluid dynamics
By leveraging advanced chemical reaction mechanisms, computational fluid dynamics (CFD), mechanism reduction, and AI-based acceleration techniques, we ensure that our simulations balance accuracy with computational efficiency. These simulations enable us to predict critical parameters such as burn rates, flame structures, and combustion stability, providing valuable insights for optimizing propellant formulations and combustor designs.
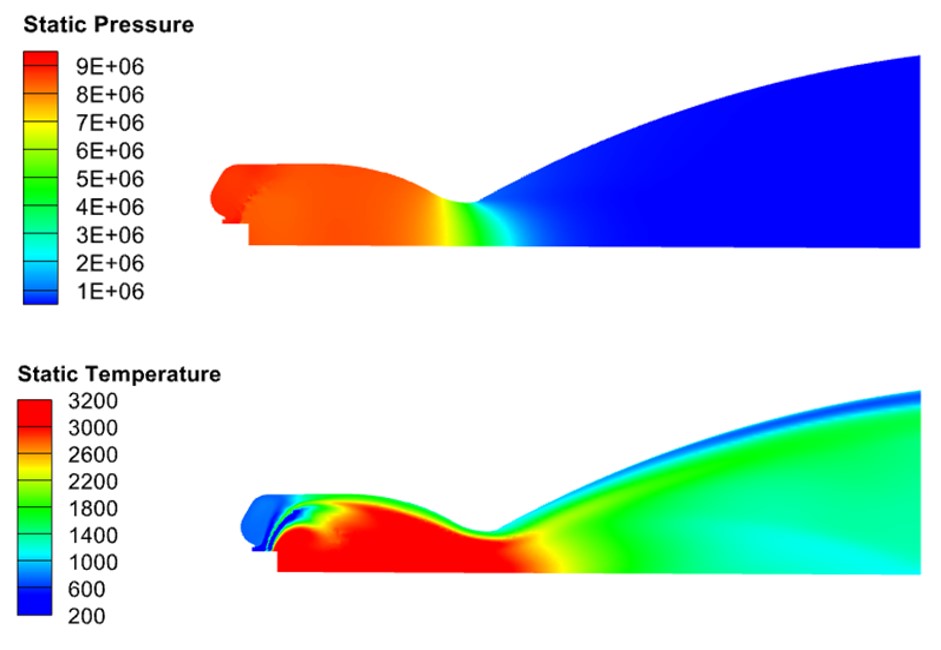
Fig. 3. CFD results of liquid rocket engine in liquid oxygen/kerosene. (On working)