Rapid compression machine
Rapid compression machine (RCM) is crucial for combustion research, as they can accurately simulate the rapid compression process of the “fuel air” mixture inside the engine, providing essential experimental conditions for studying key combustion parameters such as the self-ignition characteristics, combustion rate, and stability of the fuel. RCM is very important in the engine development process, they can simulate the compression stroke of the engine, help optimize the compression ratio, combustion chamber shape, and intake system, and play a key role in improving engine thermal efficiency, reducing fuel consumption, and pollutant emissions. The phenomenon of spontaneous combustion can be studied in a more ideal, stable, and controllable environment than reciprocating engines. The basic goal of RCM is to quickly raise the test gas to high temperature and pressure with minimal heat loss. It has a dual opposed piston configuration, with a compression time of less than 16 ms, and uses a slotted piston head to improve the post compression temperature distribution inside the combustion chamber. Figure 1 shows the physical image of the Dual-Opposed Pistons RCM at Northwestern Polytechnical University, and Figure 2 shows the overall schematic diagram of the experimental system.
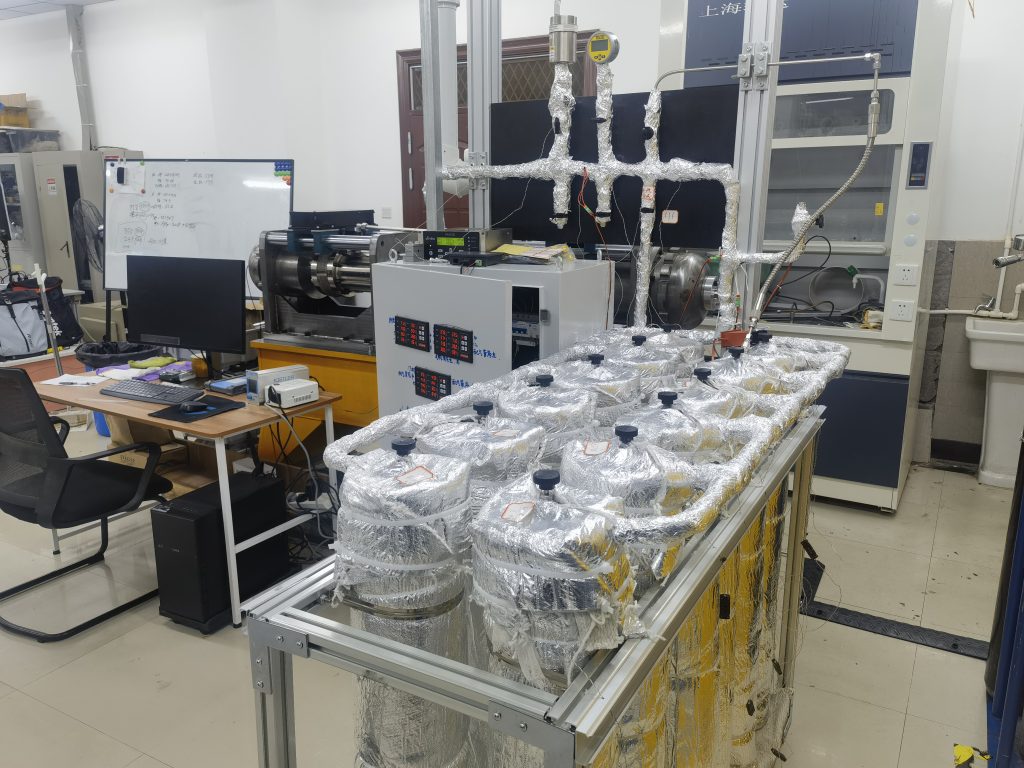
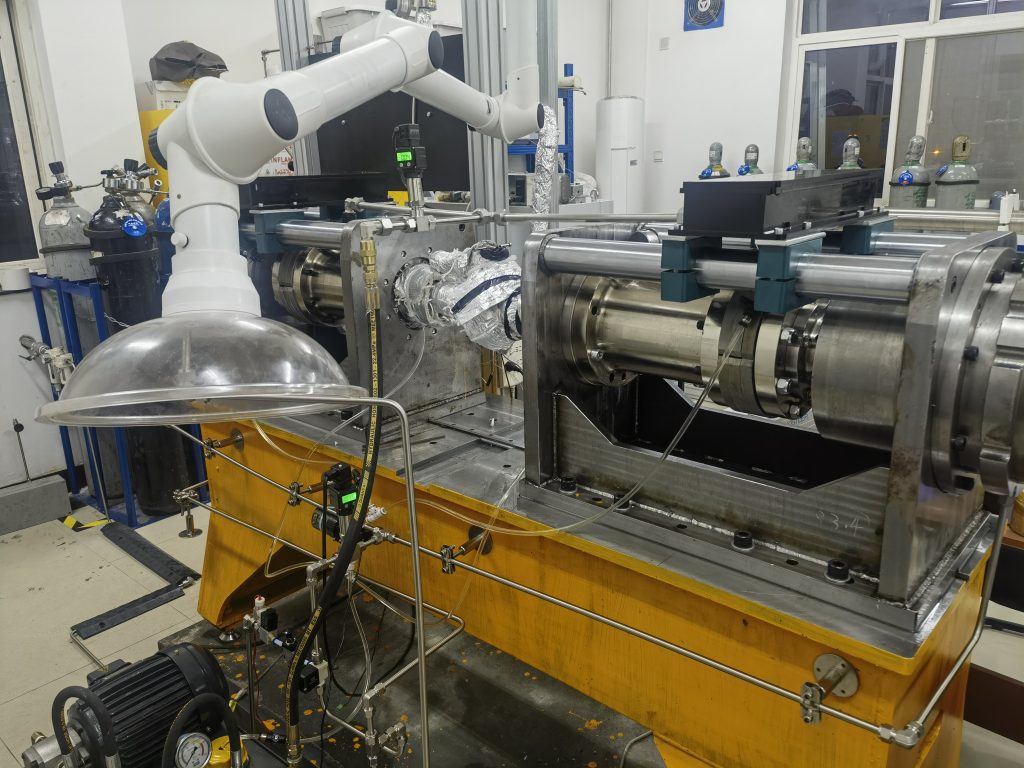
Fig. 1. Physical photo of RCM in NPU
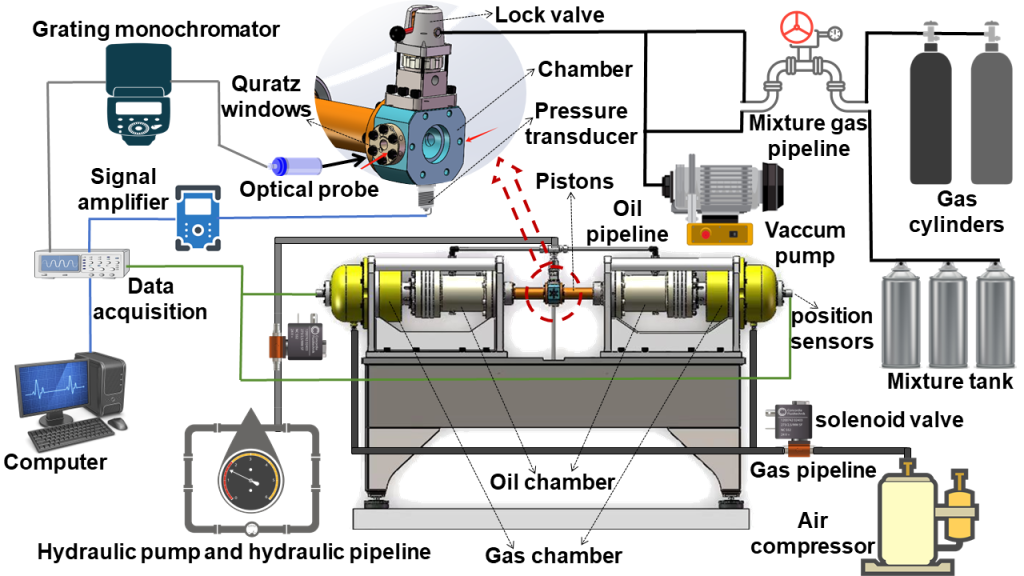
Fig. 2. Scheme diagram of RCM experimental system in NPU
The center of the RCM is the compressor body, which contains two opposed pistons that work in the compression chamber to rapidly compress gas. There are also oil reservoirs and air pressure chambers for storing hydraulic oil and compressed air respectively. On the left side of the diagram, there are data acquisition cards, signal amplifiers, and a computer for collecting and processing data during the operation of the compressor. Optical probes, a grating monochromator, and a photomultiplier tube are used to measure the optical signals inside the compressor to assist in monitoring the compression process. The oil pressure pump and oil pressure pipelines provide lubricating oil for the compressor. On the right side of the RCM, there are gas cylinders and gas – mixing tanks for storing and mixing the gases required for the experiment. The intake and distribution pipelines transport the mixed gases to the combustion chamber, which is equipped with pressure sensors for monitoring pressure changes. Built – in piston rods and position sensors are used to monitor the position and motion state of the pistons. There is also a vacuum pump for ensuring the vacuum environment of the system. The Dual-Opposed Pistons RCM rapidly compresses the gas in the combustion chamber through two pistons, obtains internal status data in real – time with the help of various monitoring devices and transmits it to the computer for analysis. Different combustion conditions are simulated by controlling temperature and pressure. Through the RCM, the ignition delay time, self – sustained combustion time, and intermediate product concentration of fuels can be measured in environments of 1 – 50 atm and 500 – 1500 K. The typical measurement results are shown in Figures 3 and 4.

Fig. 3. Scheme diagram of typical IDT definition in RCM
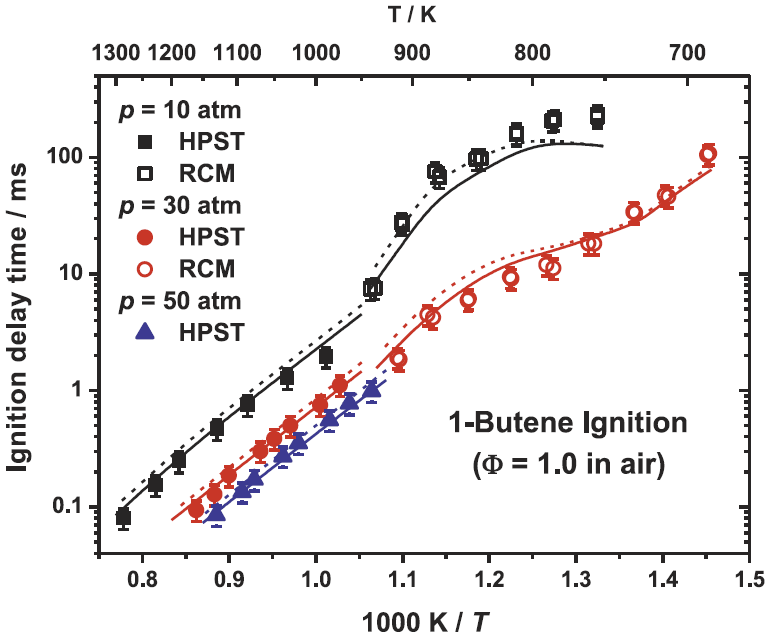